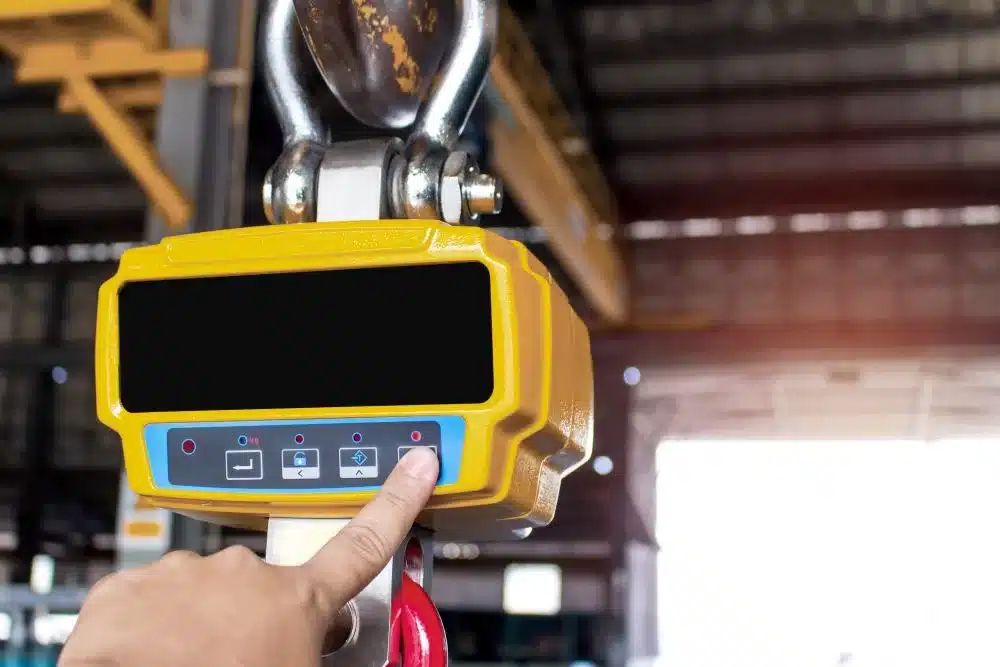
The utilization of crane scales in industrial sectors has been a common way to handle precise measurements of heavy loads for a long time.
Traditionally, these scales operated on analog mechanisms, offering reliability but lacking the advanced capabilities that digital technology now affords.
As industries evolved and demanded greater accuracy, efficiency, and connectivity, the shift to digital crane scales emerged and became the new go-to.
In this article, you will be able to explore the historical context, limitations, advantages, and other curiosities surrounding this transformation.
The Era of Analog Crane Scales
Analog crane scales were the stalwarts of weighing technology, emerging during an era dominated by mechanical systems.
They are rooted in fundamental mechanical principles, operating on physical components like springs, levers, and dials. They translated the force of the load into a readable weight on a scale.
Celebrated for their resilience, analog crane scales were designed to endure harsh conditions prevalent in sectors like manufacturing, logistics, construction, and agriculture.
Their mechanical scale setup made them extremely dependable once they didn’t rely on external power or electronic components, ensuring reliability even in environments where electrical systems might fail.
How Do Analog Crane Scales Function?
Analog crane scales typically consist of a robust framework supporting a mechanism that converts the force exerted by the load into a readable weight display.
The functioning of analog crane scales involves the application of mechanical elements such as springs, levers, and dials.
When a load is suspended from the scale, the force exerted by the load causes the springs or other tension-based components within the scale to stretch or compress.
This change in the tension or compression of the springs is directly proportional to the weight of the load.
The mechanism is calibrated in such a way that the stretching or compression of the springs translates into a corresponding movement of a pointer on a dial or a numerical display.
This movement indicates the weight of the load by pointing to a specific value on the scale.
The measurement accuracy of analog crane scales relies on the precision of the mechanical components and the calibration of the scale.
However, factors such as wear and tear of the mechanical parts, environmental conditions, and calibration drift can affect the accuracy of these scales over time.
Despite their simplicity and reliability, the reliance on mechanical components makes analog crane scales susceptible to inaccuracies and necessitates regular calibration and maintenance to ensure precision in weight measurement.
Limitations of Analog Crane Scales
The reliability and simplicity of analog crane scales were always highly praised, yet they struggle with several inherent limitations that hinder their effectiveness, especially in the context of evolving industrial demands.
1. Absence of a Digital Weighing Scale Display
Analog crane scales operated with mechanical indicators, lacking digital displays.
This absence made it necessary for operators to manually interpret weight readings, which introduced a margin of error, or, in other words, the reliance on visual estimation often led to inaccuracies in measurement interpretation.
2. Calibration Drift and Mechanical Wear
One of the primary challenges with analog scales was their susceptibility to calibration drift and mechanical wear over time.
Factors such as frequent usage, exposure to varying temperatures, and wear and tear of mechanical parts and components could affect their accuracy.
Regular recalibration was essential to maintain precision scales, requiring additional time, effort, and resources.
3. Integration Challenges with Modern Electronic Scale Systems
The inability of analog crane weight scales to provide digital output posed challenges in integrating them with modern data management systems.
The absence of digital outputs from analog scales made it cumbersome to seamlessly incorporate weight data into these modern scale systems.
This lack of integration limits the ability to analyze and utilize weight-related information effectively.
4. Susceptibility to Environmental Factors
Analog scales were vulnerable to environmental factors such as vibrations, shock, and harsh conditions prevalent in industrial settings.
These external influences could impact the accuracy of analog scale measurements, leading to inconsistencies in weight readings.
With time and the advancement of new technologies, the evident limitations of analog crane scales became more apparent despite their historical significance and reliability.
Although, it is important to note that this version was, without question, a necessary step in the evolution of digital crane scales as we know them today.
The Digital Revolution: Rise of Digital Crane Scales
With the arrival of digital crane scales, the weighing market started to steer away from analog systems’ limitations and embrace the new model’s precision and efficiency.
Amidst a period of swift technological progress, digital crane scales leveraged electronic sensors, microprocessors, and advanced algorithms to make significant advancements.
Incorporating these digital components was a big leap in the capabilities of weighing systems that now could offer real-time, highly accurate weight readings, setting new standards for the industry.
The Mechanisms Behind Digital Crane Scales
Behind a robust body, made to endure difficult environments, digital crane scales utilize electronic sensors, microprocessors, and intricate algorithms to convert the force exerted by the suspended load into digital weight measurements.
Electronic sensors detect and measure the applied force or tension, converting it into electrical signals processed by microprocessors.
The microprocessors analyze the incoming data using advanced algorithms to calculate the weight of the load accurately.
The calculated body weight is displayed digitally, offering immediate and easily interpretable readings.
Unlike analog truck or crane scales, their digital version is able to deliver clear, numeric readouts, eliminating the need for manual interpretation and reducing the potential for human errors in data recording.
With the advance of technology, digital scales now often integrate connectivity features, allowing for wireless data transmission and integration with computerized systems or IoT platforms.
This connectivity facilitates real-time monitoring, remote access to weight data, and the implementation of predictive maintenance strategies.
Advantages of Digital Crane Scales
Digital crane scales have a wide range of advantages that have transformed weighing processes across diverse industrial sectors, the main ones being:
1. Enhanced Accuracy and Precision
Digital crane scales are renowned for their superior accuracy and precision.
Utilizing electronic sensors and sophisticated algorithms, they are able to reduce the impact of factors like calibration drift and mechanical wear.
2. Instantaneous Readouts and Digital Displays
Unlike analog scales, digital crane scales provide instantaneous and easily interpretable digital readouts.
This feature eliminates the need for manual interpretation, significantly reducing the potential for human errors in reading and recording body weight data.
3. Seamless Integration with Modern Systems
The digital output of these scales facilitates seamless integration with modern computerized systems.
Digital data compatibility enables efficient recording, analysis, and management of weight-related information within existing software or IoT platforms.
4. Connectivity and Remote Monitoring
Digital scales embrace connectivity features, enabling remote monitoring and data transmission.
This allows real-time access to weight data, facilitating remote monitoring and management.
5. Adaptability and Customization
Digital crane scales are designed to cater to diverse industrial needs and provide adaptability and customization options.
They can accommodate various load capacities and operating conditions.
If your company needs a personalized crane scale project, Massload’s expert team can help. Get in touch, and let’s discuss what the best course of action for your specific needs is.
6. Automation and IoT Integration
Leveraging IoT capabilities, digital crane scales enable automation and integration with smart systems. IoT-enabled scales facilitate automated data collection, analysis, and reporting.
7. Reduced Maintenance and Calibration
Digital scales generally require less frequent calibration and maintenance compared to analog counterparts. The reduction will save your company time and money.
There are numerous advantages to the digitization of the crane scales and all of them point to how much more the industry can make and operate with this equipment that delivers more
accuracy, efficiency, and data-driven insights for better decision-making and streamlined operations.
When Did Digital Scales Come Out?
Digital scales debuted commercially in the late 1970s, initially finding use in laboratory and consumer applications.
However, their adoption in industrial settings, specifically crane scales, has no specific date.
It was a natural phenomenon that occurred alongside the advancement of other electronics and computing mechanisms in the industrial market.
Are Analog Scales More Accurate Than Digital Ones?
Contrary to common misconceptions, digital crane scales often outperform analog scales in terms of accuracy.
Digital scales mitigate issues related to mechanical wear, calibration drift, and subjective interpretations that were inherent in analog systems. The precise electronic sensors in digital scales significantly minimize errors, providing more reliable and consistent measurements.
Which Scales Are Better, Digital or Mechanical?
While mechanical (analog) scales are more robust and simple, their digital version is superior in accuracy, precision, and ease of use in industrial applications.
Comprehending the historical transition between analog and digital scales also means realizing how the industry has been evolving.
While analog scales were dependable, they had their limits, like the constant need for calibration and the necessity of collecting data by looking at a not-so-precise indicator.
On the other hand, driven by the increasing necessity of precision and efficiency in the industry, the digital scale evolved and is a reliable source of accurate weight measurement information today.
Moving from sturdy yet basic analog scales to highly precise, instantly connected, and data-driven digital systems has revolutionized how industries handle weight measurement.
Experience the Future of Crane Weighing Solutions with Massload!
Discover unparalleled accuracy, seamless integration for networked and PLC applications, and enhanced efficiency while elevating your operations and optimizing load measurements effortlessly with Massload Technologies.
Get in touch today and explore our cutting-edge crane scale solutions tailored for industries like OEMs, oil and gas, agriculture, mining, and more.