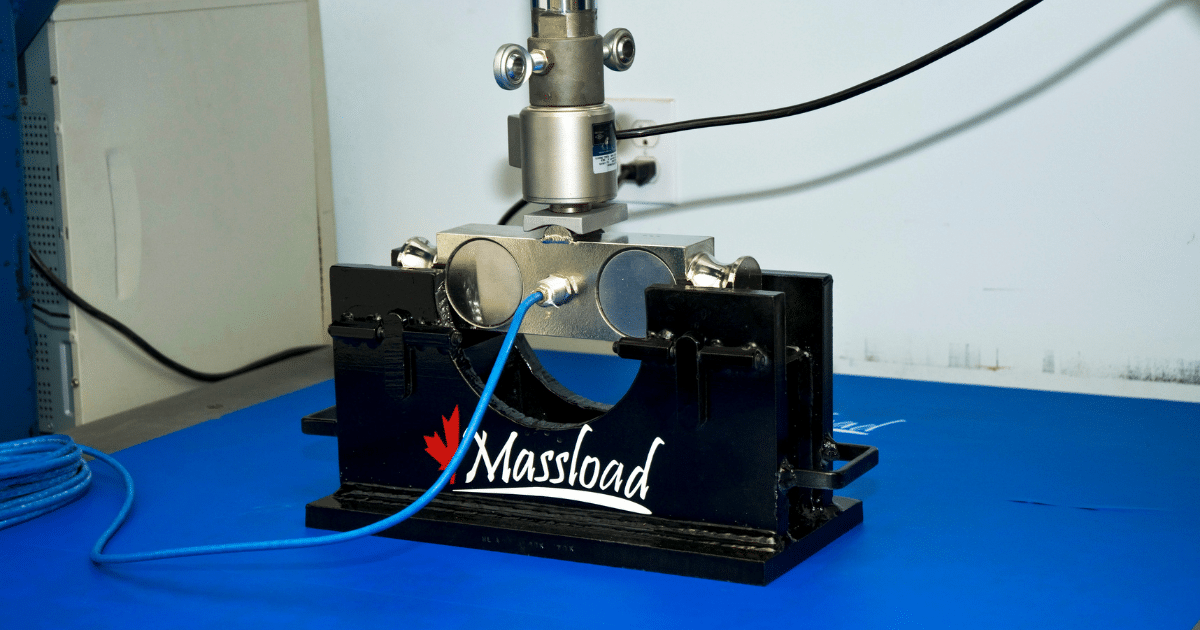
Accurate weight measurement is critical for running industrial operations smoothly and safely. At the center of this are load cells, devices that convert force or weight into an electrical signal that can be read. Calibrating these load cells is key to accuracy and reliability in many applications.
In this guide, we’ll cover load cell calibration, why it’s important for accuracy and how it applies to many industrial applications.
What is a Load Cell?
A load cell is a transducer that converts force or weight into electrical signals. This allows for precise weighing in environments ranging from smaller-scale lab setups to large-scale industrial operations.
Load cells come in different types—strain gauge, hydraulic, pneumatic, and capacitive—with strain gauge load cells being the most common. These detect strain in their gauges when force is applied and alter electrical resistance to produce proportional signals.
Why is Proper Load Cell Calibration Important?
Calibration adjusts the load cells to get accurate and reliable readings. Over time, load cells can drift from their original calibration and give inaccurate readings.
Accurate calibration is important for:
- Safety: Preventing overloading or underloading in industrial operations as per OSHA regulations for safe lifting practices such as described here.
- Efficiency: Reducing production errors which can lead to rework or rejected products.
- Regulatory Compliance: Meeting industry standards set by organizations like ISO (International Organization for Standardization).
The Importance of Calibration Across Various Applications
Before we get into the calibration process, let’s talk about the challenges that affect load cell accuracy. Mechanical wear, environmental factors and frequent use can cause calibration drift and inaccurate readings especially in harsh environments. Calibration is required across all load cell applications, from manufacturing to aerospace, to ensure performance.
Load Cell Applications
Load cells are used across many industries. Here’s how calibration ensures accuracy in:
1. Manufacturing & Production of Load Cells
Load cells weigh products on conveyor belts and verify material weights during packaging. Calibration ensures smooth production runs and prevents errors that can lead to bad products.
2. Truck Weighing Systems
In weighbridges and truck scales, load cells weigh vehicles and cargo. Calibration is critical to prevent overloading and to meet legal requirements and safety standards.
3. Healthcare & Medical Devices
Load cells are used in healthcare, especially in devices like hospital beds, infusion pumps and patient lifts. Precision is critical in these applications to ensure patient safety and comfort. Load cell calibration ensures devices measure weight or force accurately and prevents potential risks or misdiagnosis.
4. Agriculture & Livestock Weighing
Load cells are also used in agricultural applications to weigh livestock, crops and feed. Calibration helps farmers track and manage resources efficiently, whether they’re weighing cattle for market or monitoring feed levels. A calibrated load cell gives you reliable data, better livestock management and more accurate yields.
5. Automotive Industry
Load cells are used in crash testing and vehicle design to measure force and weight in various scenarios. For example, load cells measure the impact force in crash test dummies. These readings need to be extremely accurate to meet vehicle safety standards, which requires frequent calibration of load cells.
6. Aerospace & Defense
In aerospace, load cells are used to test aircraft components, measure aerodynamic forces in wind tunnels and weigh satellites and space vehicles. Calibration in these applications is critical for safety and mission success and to account for even the smallest of errors.
Crane Scales Calibration Challenges
While crane scales is just one of the many applications, it deserves special mention as it’s a critical part of lifting operations. Crane scales use load cells to measure the weight of suspended loads during lifts to ensure the crane operates within safe limits.
- Mechanical Wear: Crane operations are heavy duty and load cells are exposed to mechanical wear so recalibration is a must.
- Environmental Factors: Crane scales are often outdoor or in harsh industrial environments which increases the chance of calibration drift due to temperature, dust or moisture exposure.
How to Calibrate a Load Cell
Now that we’ve discussed the importance of calibration, let’s get into how to calibrate a load cell. The calibration process involves a few steps to ensure accurate readings. Here’s how it works:
1. Apply Known Loads
Calibration starts by applying known loads to the load cell. These calibrated weights or force standards are the references to measure the output accuracy of the load cell.
2. Compare Output Readings
Next, the output readings of the load cell are compared to the expected values based on the applied loads. Any variations or errors are noted for further adjustment.
3. Adjust for Accuracy
After identifying the errors, technicians adjust the load cell to fine-tune its performance. This may involve changing internal settings or recalibrating the output to match the known values.
Recalibration helps to correct for drift caused by environmental factors, wear and tear or mechanical impacts. Calibration should be done based on how often the load cell is used and the operating environment.
What is Two-Point vs. Multipoint Calibration?
Load cell calibration has two main methods: two-point calibration and multipoint calibration.
Two-Point Calibration
In two-point calibration, adjustments are made at two reference points (usually zero and one other load value). While this is quick, it may not account for non-linearities across the load range.
Multipoint Calibration
Multipoint calibration involves adjusting the load cell at multiple points across its capacity range to get more accurate results by addressing non-linearities at different stages.
Choosing the right calibration method depends on the precision required, application and industry standards.
What Causes Load Cells to Lose Calibration?
Load cells can lose calibration over time and often need recalibration. This is called drift and it’s caused by:
- Frequent Use: Load cells used continuously or under high stress may experience more drift.
- Environmental Conditions: Temperature changes, humidity and vibrations can affect a load cell’s accuracy.
- Wear and Tear: Over time mechanical wear can cause performance degradation and requires recalibration.
At Massload, we recommend an annual calibration for most load cells to ensure optimal accuracy and reliability.
Practical Tips to Maintain Accuracy
Maintaining load cell accuracy is more than just calibration. Here are a few tips to help with maintaining accuracy for as long as possible:
- Routine Inspections: Inspect load cells regularly for visible damage, corrosion or signs of wear. Even small issues like bent connectors or moisture exposure can affect calibration and overall performance.
- Environmental Protection: Use protective housings or enclosures to shield load cells from harsh environments like extreme temperatures, humidity or excessive dust.
- Periodic Calibration: Stick to a calibration schedule, especially if load cells are used in critical applications. Testing with known weights will detect drift early and correct it.We always recommend an annual recalibration to maintain optimal accuracy.
- Proper Handling: Handle load cells carefully and avoid exposing them to shock, vibrations or overloading. Train operators on proper load cell handling to minimize the risk of damage.
- Maintenance Records: Keep a record of calibration intervals, adjustments and any maintenance done. These logs will track the condition of the load cells and provide valuable data for future calibration needs.
Should You Calibrate In-House or Outsource?
Load cell calibration can be done in-house or outsourced depending on your resources and expertise. In-house calibration saves cost and gives you more control but requires skilled personnel and equipment maintenance. For businesses with limited resources, maintaining high standards can be a challenge.
Outsourcing to specialists gives you access to advanced tools and expert knowledge to ensure industry standards. This is ideal for critical processes where precision is key. Consider your budget, frequency needs and in-house capabilities before you decide. Calibration ensures accuracy, efficiency and safety.
Get Precision with Professional Load Cell Calibration Services
Load cells are used in many industries from manufacturing and healthcare to aerospace and agriculture. Whatever the application, accurate load cell calibration is the common denominator for safety, efficiency and compliance.
At Massload Technologies, we offer calibration services to meet the needs of various industries. Whether you’re working with tension or compression load cells, our state-of-the-art equipment and expert technicians ensure pinpoint accuracy every time.
We use Morehouse reference load cells that are regularly recalibrated and traceable to NIST standards for the highest level of precision. Each calibration includes a detailed certificate with all the data you need to track your load cell’s performance over time.
Contact us today to learn more about our calibration services and how we can help you maintain the accuracy of your load cells.