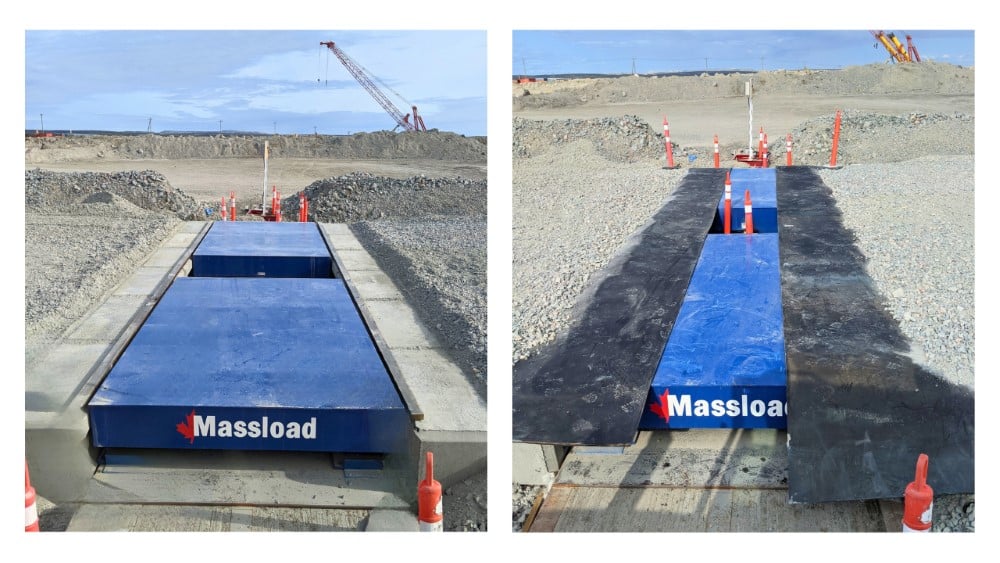
For surface mining operations, the best truck scale is typically a heavy-duty truck axle scale designed for high-capacity, off-road vehicles.
Whether you’re operating a long-term mine or a temporary exploration site, your scale must withstand extreme weights, rugged terrain, and harsh weather—a combination that creates a perfect storm where standard weighing equipment often fails outright or degrades rapidly within weeks or sometimes days.
This guide outlines the best mining truck scales, their pros and cons, and the key factors to consider before investing in one of these specialized measurement systems engineered for mining’s unique challenges.
What Are the Critical Requirements for Mining Truck Scales?
1. Weight Capacity for Mining Vehicles
Mining trucks haul extreme payloads — often exceeding 250 tons. This isn’t your standard highway trucking; we’re talking about machines that cost $3-5 million each and carry loads that would crush conventional scales.
Choose a truck scale with a rated capacity at least 20% more than the gross weight of the truck scale to the scale’s full capacity.
With structural reinforcement to handle oversized vehicles like articulated or rigid-frame dump trucks.
The technical challenge isn’t just the high capacities but maintaining accurate measurements despite:
- Uneven weight distribution
- Dynamic effects from vehicle positioning
- Temperature variations in the operation
- Debris buildup
2. Durability in Harsh Conditions
Mining environments represent some of the most challenging conditions for weighing equipment, creating a uniquely hostile environment for precision measurement. Operations face extreme temperature swings, abrasive dust, and punishing vibrations that standard vehicle scales can’t handle. Look for mining truck scales with:
- Steel or concrete deck construction with generous safety factors for shock and overload protection
- IP-rated load cells with multiple sealing methods for dust and water resistance
- Surface corrosion-resistant coatings specifically engineered for prolonged exposure to mining conditions
Standard industrial scales simply aren’t engineered for these conditions. The standard scale’s sealing methods are inadequate, have limited temperature compensation, and have insufficient structural strength. The result? Erratic measurements, progressive drift, and eventual catastrophic failure—often at the worst possible moment operationally.
3. Weighing Accuracy
Accurate weight data helps prevent overloading, correct billing costs, manage inventory, and ensure regulatory compliance. In the mining industry, weight measurements translate directly into revenue calculations and regulatory documentation. Prioritize:
- Load cell with the lowest combined % error and a wide range of temperature compensation
- Legal-for-trade certification (if weights are used for commerce)
- Signal conditioning module with the lowest linearity % error, a wide range of operating temperatures, and good ADC performance.
The fundamental principle remains consistent with standard weighing technology, but the implementation must address the unique challenges of mining environments where electromagnetic interference from high-powered equipment can corrupt measurement signals.
4. Deck Size and Configuration
Ensure your scale can fully accommodate the size of your mining vehicles:
- Standard mining truck scales range from 30 to 100+ feet in length
- Choose extra-wide platforms if using oversized equipment
- Consider approach requirements for efficient vehicle positioning
The fundamental principle remains consistent with standard weighing technology, but the implementation must address the unique challenges of mining environments where electromagnetic fields from high-powered equipment cause interference to the measurement signals.
5. Installation Type
- Surface-mounted truck scales: Easier and faster to install; require ramps but provide excellent accessibility for maintenance and inspection
- Pit-mounted truck scales: Flush with the ground; ideal for space-constrained or permanent sites but require more extensive site preparation and drainage consideration
For operations in regions with extreme weather, installation type directly impacts both the initial performance and long-term reliability of your weighing system.
6. Portability
- Fixed weighbridge scales: Best for long-term, high-traffic sites where consistent, high-volume weighing justifies permanent infrastructure investment
- Portable axle pad scales: Better for temporary, remote operations where flexibility matters and site conditions change regularly
These portable truck scales eliminate one of the most common failure points in traditional measurement systems, permanent installation limitations, while simplifying relocation when operational requirements change.
7. Data Integration & Automation
Modern scales serve as the data gatekeepers of mining operations, providing critical information that flows throughout your management systems. Look for mining truck scales with:
- Remote monitoring capabilities for centralized oversight
- Automated data logging for compliance documentation
- Cloud or SCADA system compatibility for enterprise integration
- Mobile interfaces provide maintenance personnel with real-time access to measurement data anywhere in the operation
For multi-site operations, centralized monitoring and analysis can optimize operations across numerous locations while ensuring consistent data quality.
8. Maintenance and Service Access
Choose a mining scale with easy-to-access junction boxes, removable covers, and modular components to minimize downtime and service costs. Mining-grade truck scales should incorporate:
- Simplified calibration verification procedures
- Protection for critical electronics and connections
- Modular design allowing component replacement without complete system downtime
- Documentation systems for maintenance history and performance trends
Through proper maintenance access design, mining operations ensure their measurement systems continue to provide the accurate, reliable data essential for both operational efficiency and safety compliance.
9. Safety Features
Protect your equipment and operators with:
- Overload protection systems that provide immediate notification of abnormal loading conditions
- Guardrails and non-slip surfaces to prevent personnel accidents during wet or icy conditions
- Compliance with regional safety regulations specific to mining applications
- Integration with site-wide safety systems for coordinated emergency response
These safety capabilities translate directly to improved protection, reduced operating risks, and enhanced productivity in increasingly competitive global markets.
Types of Truck Scales Used in Surface Mining
Here’s a comparison of the most common scale types and where they perform best:
Type of Mining Truck Scale | Best For | Drawbacks |
Portable Axle Scales | Remote or temporary mining projects in exploratory operations or short-term extractions where infrastructure investment isn’t justified | – Not ideal for full-vehicle weighing;
– Less throughput capacity; – Requires more operator involvement. |
Weighbridge Truck Scales | Applications where legal-for trade is a requirement. | – Require substantial foundations and more space;
– Higher initial investment; – Less flexibility for site changes. |
Modular Truck Scales | Relocatable setups or semi-permanent sites where operational needs may evolve or mining activities shift location | – Slightly less robust than fixed designs;
– Require careful site preparation to maintain accuracy; – More susceptible to settlement issues. |
Onboard Truck Scales | Real-time tracking during haulage where immediate feedback improves loading efficiency and prevents overloading | – Lower precision than static weigh stations;
– Requires more maintenance due to exposure to vehicle vibration; – Higher per-vehicle cost. |
Wheel Weighers | Quick spot-checks in remote or off-road areas where verifying approximate weights is sufficient for operational decisions | – Not suitable for ultra-heavy mining loads;
– Significantly lower precision; limited durability in harsh conditions; – Primarily for compliance verification. |
Final Recommendation
For temporary or exploratory sites, a portable axle pad scale offers flexibility, faster setup, and lower upfront investment, though it may sacrifice some speed.
These systems allow operations to maintain essential weight verification without committing to permanent infrastructure, particularly valuable during site development or limited-duration extraction activities.
For long-term surface mining operations, a full-length weighbridge truck scale with a steel deck, digital load cells, and system integration capabilities can be the best option. These scales are rugged but will cost you a lot more.
Ready to Find the Right Truck Scale for Your Mining Operation?
Choosing the right truck scale can make a major impact on your efficiency and bottom line. Implementing properly engineered weighing technology specifically designed for mining applications represents one of the most effective operational improvements available to modern mining operations.
Need expert advice or help to customize a scale for your mining environment? Contact our team today to speak with an engineer or request a quote tailored to your operation.