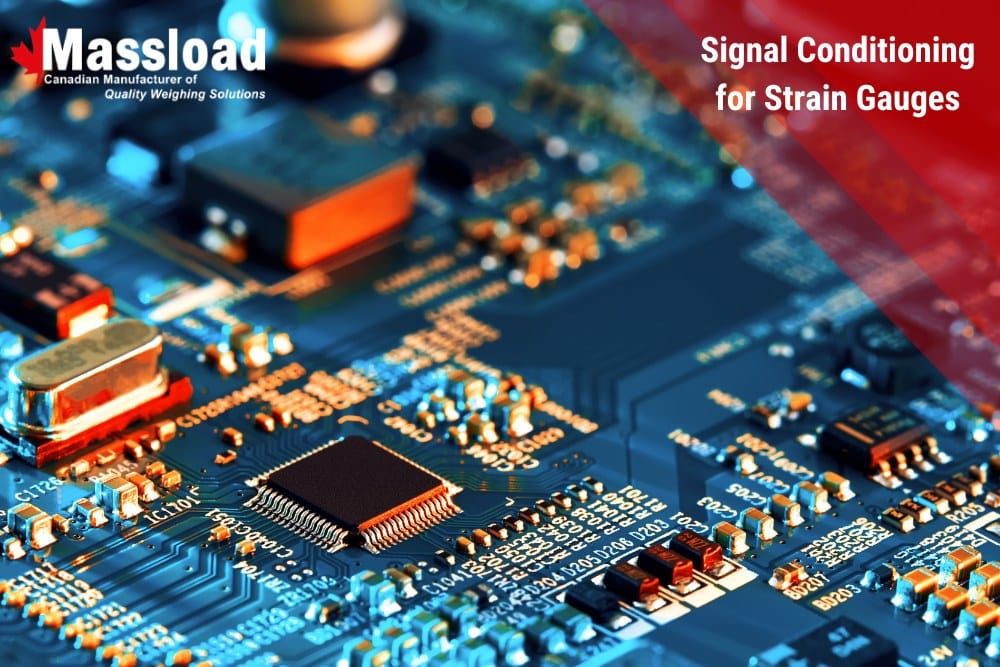
At the heart of precision weight measurement lies the strain gauge—a small but powerful sensor that translates mechanical strain into measurable electrical signals.
But the journey from strain to signal isn’t straightforward; it requires sophisticated signal conditioning circuits to amplify, filter, and convert these delicate signals into actionable data.
This article delves into the intricacies of strain gauge bridges and the technology that transforms subtle deformations into reliable measurements that drive industries forward.
What is a Strain Gauge Bridge?
A strain gauge is a sensor used to measure strain (deformation) in an object. When an object deforms due to an applied force, its shape changes slightly. A strain gauge detects this deformation by changing its electrical resistance, which can then be measured and related to the amount of strain.
How It Works:
- Structure: A strain gauge typically consists of a thin, flexible backing that supports a metallic foil pattern. This pattern is designed to maximize the change in resistance when the gauge is stretched or compressed. The gauge is usually bonded to the object that is being measured using a special adhesive.
- Operation: When the object to which the strain gauge is attached experiences a force, it deforms slightly. This deformation causes the strain gauge to stretch or compress, which in turn changes the length and cross-sectional area of the metallic foil. These changes alter the electrical resistance of the strain gauge.
- Measurement: The change in resistance is proportional to the strain experienced by the object. This small change in resistance can be measured using a Wheatstone bridge circuit, which converts the resistance change into a measurable voltage signal. The voltage signal is then analyzed to determine the amount of strain.
Applications:
Strain gauges are widely used in various fields, including:
- Engineering and Construction: To monitor the strain in structures like bridges, buildings, and dams, ensuring they are safe and structurally sound.
- Mechanical Testing: To measure the strain on components such as beams, gears, or machinery parts under load.
- Aerospace and Automotive Industries: To test materials and components for durability and performance under stress.
- Medical Devices: As a sensor component within a load celIn devices that monitor the forces applied to prosthetics or in research for biomechanics.
Types of Strain Gauges:
- Metallic Strain Gauges: These are the most common type, where the sensing element is a metal foil. They are widely used in industrial applications.
- Semiconductor Strain Gauges: These offer higher sensitivity compared to metallic gauges but are more sensitive to temperature changes, which can be a disadvantage in some applications.
What Does Signal Conditioning Circuit Mean?
A Signal Conditioning Circuit is an electronic system used to modify a signal in a way that prepares it for the next stage of processing. This involves converting the signal from a sensor or transducer into a more usable form. Signal conditioning circuits are crucial in various applications where accurate and reliable data measurement is required.
Here’s a breakdown of what it typically involves:
- Amplification: Often, the signal from a sensor is too weak to be processed effectively, so it needs to be amplified. Signal conditioning circuits can increase the amplitude of the signal to make it more robust and easier to analyze.
- Filtering: Signals can contain noise or unwanted frequencies that can interfere with the measurement. Filtering removes these unwanted components, ensuring that only the relevant part of the signal is processed.
- Isolation: In some cases, electrical isolation is necessary to protect the signal source from high voltages or other harmful conditions. Isolation also helps eliminate ground loops and reduce interference.
- Linearization: Some sensors do not have a linear relationship between the measured parameter and the output signal. Signal conditioning circuits can linearize the output, ensuring that the signal accurately reflects the measured value.
- Conversion: Signals may need to be converted from one form to another, such as from analog to digital or from one voltage range to another, to be compatible with the subsequent processing equipment.
Which Signal Conditioning Circuit is Ideal for Strain Gauges?
A strain gauge signal conditioner with bridge excitation is designed to convert the small electrical signals generated by the strain gauge into a more usable and accurate form, typically for measurement and analysis purposes. Strain gauges are used to measure deformation (strain) in materials, and the output signal is typically a very small change in resistance, which requires careful amplification and processing. Here’s a breakdown of the components and functions typically involved in a signal conditioning circuit for a strain gauge:
1. Wheatstone Bridge Configuration
Strain gauges are often used in a Wheatstone bridge configuration, which is a circuit that allows for precise measurement of small changes in resistance. The Wheatstone bridge consists of four resistive arms, one or more of which are strain gauges. This configuration converts the small resistance change of the strain gauge into a voltage change that can be measured.
Depending on the application and sensitivity required, the Wheatstone bridge can be configured in any of these setups:
- Full Bridge: Four active strain gauges
- Half Bridge: Two active strain gauges and two fixed resistors
- Quarter Bridge: One active strain gauge and three fixed resistors
2. Excitation Voltage
The excitation voltage is applied to the Wheatstone Bridge. This is a stable DC voltage supplied to the bridge to power the strain gauges. The stability and precision of the excitation voltage are crucial because any variation in this voltage can affect the accuracy of the measurement.
AC voltage can also be used as an excitation source to minimize offset voltage. This AC excitation technique employs external switches to alternate the polarity of the bridge excitation. It’s important not to confuse this with excitation using a genuine AC signal. In this method, the system takes one measurement with forward polarity and another with reverse polarity, then averages the two to produce a single conversion result that is almost entirely free of offset.
3. Signal Amplification
The output signal from the Wheatstone bridge typically has a very small differential voltage. Strain gauge amplifier is used to amplify this small signal to a level that is suitable for further processing or digitization. Instrumentation amplifiers are chosen because they provide high gain, excellent common-mode rejection, and low noise, which are essential for accurately amplifying the small signals from the strain gauge. The most common bridge amplifiers produce 0-10V output or 4-20mA output.
4. Filtering
Low-pass filters are often employed to remove high-frequency noise from the signal. This is important because the signal from the strain gauge can be affected by electrical noise, vibrations, or other sources of interference.
5. Zero Balance and Temperature Compensation
Zero balance circuitry may be included to nullify any initial offset voltage that exists when there is no strain. This ensures that the output signal corresponds accurately to the strain being measured.
Temperature compensation is important because strain gauges are sensitive to temperature changes, which can cause errors in measurement. Temperature compensation can be achieved using dummy gauges or additional circuitry to correct for these effects.
6. Analog-to-Digital Conversion (ADC)
In many modern applications, the conditioned signal is then fed into an Analog-to-Digital Converter (ADC) for digitization. This allows the signal to be processed by a microcontroller, computer, or other digital system for further analysis, logging, or display.
7. Calibration
The signal conditioning circuit might also include calibration adjustments to ensure that the output corresponds accurately to the actual strain being measured. This could involve setting gain and offset parameters to match the characteristics of the specific strain gauge and application.
These components work together to ensure that the small and delicate signals generated by the strain gauge are accurately and reliably converted into a form that can be easily measured, analyzed, and used in various applications, such as structural health monitoring, industrial measurement, and more.
What Type of Signal Does a Strain Gauge Output?
A strain gauge typically outputs a small change in electrical resistance in response to mechanical deformation (strain). This change in resistance is very slight and needs to be converted into a more measurable form, typically a voltage signal, using a Wheatstone bridge configuration.
Here’s how it works:
Resistance Change
When a strain gauge is bonded to an object, any deformation in the object (such as stretching or compressing) causes the strain gauge to deform as well. This deformation changes the length and cross-sectional area of the strain gauge’s conductive material, leading to a change in its electrical resistance. The amount of resistance change is proportional to the amount of strain.
Voltage Signal
Strain gauges are usually integrated into a Wheatstone bridge circuit to measure this small change in resistance. The Wheatstone bridge converts the small resistance changes into a small differential voltage signal. This voltage signal is directly related to the amount of strain experienced by the gauge.
Nature of the Signal
The output signal from a strain gauge in a Wheatstone bridge is a small, typically low-millivolt-range differential voltage that varies as the strain changes. This small voltage signal often needs to be amplified and conditioned before it can be used for further processing or analysis.
Conclusion
You’ve just unlocked the secrets behind strain gauges and the clever circuits that turn tiny tweaks into reliable data.
Whether you’re tweaking designs or solving engineering puzzles, you’ve got the tools to make every measurement count.
But why stop now? Dive into more of our articles and keep pushing the boundaries of what’s possible—because in the world of precision, there’s always another level to reach.
For expert advice or assistance with your specific application, don’t hesitate to contact Massload. We’re here to help you achieve the highest accuracy in your measurements.